Kodak Lens provides innovative spectacle lens products and some of the most advanced spectacle lens technology in the world. As one of the largest providers of spectacle lenses in the UK, we have been servicing opticians for almost two decades. Our global research and development teams are constantly working to develop the ultimate materials and designs.
The importance of lenses often gets overlooked when people are choosing their new spectacles. Frames are obviously important to the aesthetic appeal, but many people are unaware of the lenses available and how what they can offer to give you greater vision. There are over 30,000 product lines in stock at the UK Kodak Lens Laboratory at any one time and Vision Value opticians will prescribe the most suitable products, depending on lifestyle and prescription requirements.
All Kodak Lenses receive a two-year manufacturing warranty under normal wear and tear.
The Lens Index. What is it and how it helps you
The thickness of your lenses is known as the index, which is used to measure the different lens materials. They range from 1.498 refractive index (the standard plastic lens) to 1.74 refractive index, the world's thinnest plastic lens material. As a rough guide, the higher the index the thinner the lens will be.
Kodak Lenses and the vision conditions they can help correct
Everyone could benefit from gaining a greater understanding of lenses and the conditions that they can help with. We aim to give you a little more information to help you at your next optician's appointment.
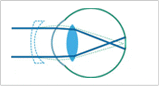
Short-sightedness or Myopia
Short-sighted people will usually see near objects clearly, but may have difficulty focusing on distant objects. Myopia is caused by the optical lens being too strong causing the focal point to move in front of the retina. A spectacle lens will correct this (green lines in diagram).
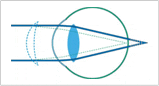
Long-sightedness or Hyperopia
Long sighted people will usually find it harder to focus on objects close to them such as a book, but may have less difficulty on focusing on the objects further away. Hyperopia is caused by the optical lens being too weak, bringing the focal point behind the retina. A spectacle lens will correct this (green lines in diagram).
Astigmatism
This is usually caused by an irregularly shaped cornea and can cause unfocused vision at all distances for portions of the field of vision. Astigmatism may occur alongside either Myopia or Hyperopia.
Presbyopia
Presbyopia is a perfectly natural and very common eye condition which we usually first notice when we do close work. It is caused by the aging process; the muscles of the eye become less flexible and we start to find it harder to focus.
How we make Kodak Lenses
There are many technical processes that go into making a Kodak Lens and making them precise to your prescription and to your lifestyle.
Step 1: Semi-Finished Lenses
The lenses that are stored in our UK warehouse are semi finished. These lenses are produced in our manufacturing plants around the world, by injecting molten monomer into optical moulds which are then cured to give a semi finished lens with a perfect front surface with a precise optical curve on it.
The back surface of the lens will be processed in our laboratory to a given curve. The combination of the moulded front curve with the processed back curve produces a lens of a given prescription.
A semi finished lens could be used as the starting point for lenses of many different prescriptions - the finished prescription will be determined by the amount of material that is processed away from the back surface and the curve that is left on this surface.
Step 2: Lens Design
After your Optician has tested your eyes and determined the prescription of the lenses you will require for your spectacles, and you have decided with him/her which type of Kodak Lenses will be best for you, they will take a number of facial measurements from you such as the distance between your pupils, to ensure the correct fit.
Our skilled Lens Technicians will then computer generate the best design for your lenses in terms of their appearance and optical performance - they calculate exactly how we will process the back surface of the semi finished lens.
Step 3: Blocking
The perfect front surface of the semi finished lens is masked and protected throughout the lens production process. A metal 'fixing block' is attached to this surface at a very precise angle which is determined by your prescription. This 'block' allows the lens to be held in the generators in exactly the right position to produce the right lens curves for your prescription.
Step 4: Generating and Smoothing
The 'blocked' lenses go into the generating machines individually.
The required curves are entered into the generators and automatic cutters then grind away, then smooth the back surface of the lens until the curves are exactly right for your prescription.
Step 5: Polishing
The back surfaces of your lenses are now polished using specialist polish and polishing pads so that a perfect back surface is created to match the still protected finished front surface.
The lenses are checked and inspected at each stage of production - cleaning is carried out using water and compressed air and handling is kept to a minimum.
Step 6: Quality Control
The lenses next go through a thorough checking procedure to make sure that they precisely match the power and specifications that your Optician has ordered for you and that the lens surfaces are perfect.
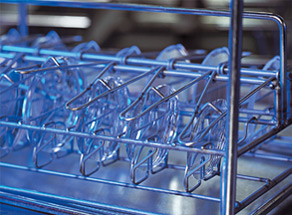
Step 7: Coatings
Next stop for your lenses is the dust-free, space age environment of the Kodak CleAR Lens Coatings laboratory. Here the lenses go through a thorough cleaning and drying process - they are placed in special holders, dipped into a series of ultrasonic tanks and are then oven dried for some 4 hours.
Step 8: Kodak CleAR lens coating
Some lenses will just have a scratch resistant coating applied to them, but more and more people choose to have a Kodak CleAR or Clean'N'CleAR anti reflection Lens coating applied, as this makes the lenses much better to look at, and to look through, as there are no distracting reflections.
Kodak CleAR and Clean'N'CleAR anti reflection Lens coatings are applied to your lenses in a high-pressure vacuum chamber. They are produced by the precise deposition of specially selected chemicals on the lens surface - 12 layers are applied to each side of the lens in a fully automated, computer controlled process. It is hard to believe but the thickness of this coating is less than 3 microns (i.e. less than the width of an average strand of hair).
Step 9: Glazing
Once your lenses have been coated, they will then be cut to the right shape for your frame using computer controlled glazing equipment - an automatic tracer follows the inside rim of your frame telling the machine the shape required, your measurements are entered and the edging machine then 'edges' the lens to the required shape.
Step 10: Finished Lenses
After a final thorough inspection your lenses are carefully packed and despatched to your Optician who fits them into your chosen frames to complete the fitting procedure.
In most cases the lenses are protected by RLX Plus (The World's most scratch resistant plastic lens surface) and come to you complete with a Two Year Guarantee.